The curing oven is dispatched complete, and requires no initial setup process, below will be a breakdown of how to change the temperature and how the curing process works.
Direct-to-film (DTF) curing ovens are specialized equipment used to cure DTF powder applied on printed films. These ovens work by maintaining a controlled environment with precise temperature settings to ensure the powder melts and adheres properly to the film. The curing process begins when the printed film, coated with DTF powder, is placed in the oven. As the temperature rises, the powder undergoes a phase change, melting and forming a solid, durable layer. This ensures the design remains vibrant and securely bonded to the fabric when transferred. The temperature must be carefully regulated; too low and the powder won’t fully melt, too high and it may cause degradation or damage to the film and the design. The precise control of temperature in DTF curing ovens is crucial for achieving high-quality, long-lasting prints.
Temperature Setting
Press the “Set” button once to display the flashing numbers. Once numbers are flashing you may use the up and down button to change the set value (SV) which is the desired temperature of the oven. The precise value (PV) is the current temperature of the oven. The left button allows you to move from the ones column to the tens, hundreds, and thousands. We do not recommend this option as temperature adjustments are usually under 10°C. Once you have learned how to adjust the temperature of the oven you are free to continue down to our testing and recommended settings below.
The size of the print and the amount of ink used in direct-to-film (DTF) transfers significantly affect the curing process. Larger prints and designs with heavy ink layers require longer curing times or higher temperatures to ensure the ink and DTF powder fully melt and adhere properly. This is because the increased volume of ink takes more time and heat to reach the optimal curing state. Conversely, using lower temperatures for smaller prints or those with less ink can result in more even and consistent prints, as there is less material to cure, and the risk of overheating is minimized. Balancing these factors—print size, ink volume, and curing temperature—is essential for producing high-quality, durable DTF transfers without compromising the integrity of the design or the substrate.
Curing Oven Time and Temperature Reference
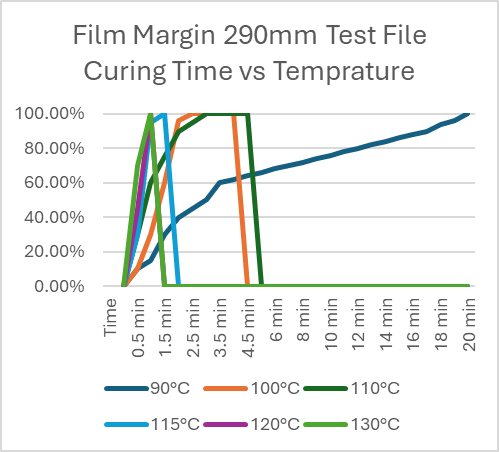
The vertical axis refers to the test prints cured amount. At 100% the print is completely cured whereas at 0% the print has not been cured or over-cured. To assess the data shown in figure _ it can be seen that @ 90°C it will take the film margin 290mm test file roughly 20 minutes to be 100% cured. @ 100°C it will take this file about 2.5 minutes (150sec) to reach a cured state, if left in the oven at @100°C for another 2 minutes the print should remain cured and not become over-cured any longer and prints tend to deteriorate and become over cured. @110°C it can be determined that the print will cure in 3 minutes and overcure by 5 minutes. @115°C we expect a full cure around 1.5 minutes but will quickly over-cure if left for much longer. @120°C We can see the print was cured at 1 minute but was over-cured at 1.5 minutes. Results did not differ for 130°C.
From this data, we would recommend setting the oven to 110°C for prints with similar ink coverage.
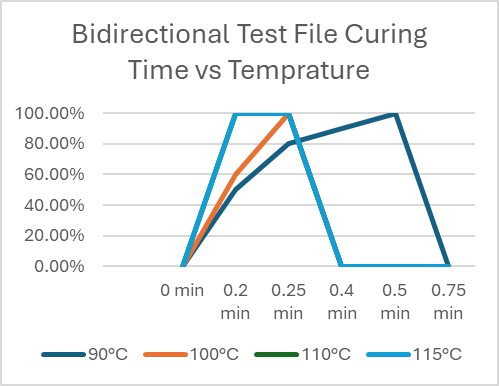
The bidirectional test file is a minuscule file to test the extremes of curing times depending on temperature. At 90°C this print will take on average 30 seconds to cure while at 100°C it will take around 20 seconds to cure. This pattern continues with 110°C & 115°C as they are expected to cure in less than 12 seconds. If the print was to be left in the over at any of the temperatures tested (excluding 90°C) it would be expected to become over-cured at 15 seconds.
The recommended temperature setting for a single file of this size would be 90°C to allow for the most consistent results.
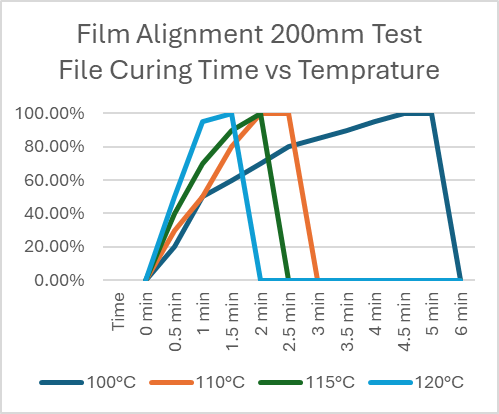
The film alignment 200mm test file was tested to gauge the optimal time and temperature for a larger ink coverage. At 100°C the print was cured in 4.5 minutes and overcooked by 5 minutes. Speeds increased for the higher temperatures where 110°C was cured in 2 minutes and over-cured by 3 minutes. 115°C is expected to cure in the same time as 110°C but will over-cure quicker. While this print at 120°C will be cured at 1.5 minutes it will be entirely over-cured by 2 minutes. This data indicates that files with similar ink coverage values are expected to cure between 1.5 minutes to 4.5 minutes.
The recommended settings for this file and similar files would be around 110°C as the curing process will be quicker than the printing process with less chance of over-curing.
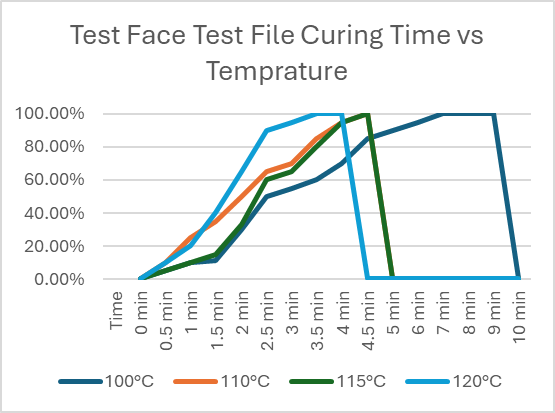
The test faces test file was utilized during testing to test the extreme point of a full coverage file the maximum size of the oven. With the file size 30cm wide by 38cm in length, this transfer covered the entire oven bed. Through testing this file, it was determined that large prints of this size require adjustment during the curing process to avoid over-curing the central area of the print. Refer to table _ on the movement timings for each temperature.
To decipher the data the test faces test file was cured at 100°C, with three movements the curing process was complete at 7 minutes and remained useable until 9 minutes in the oven. At 110°C & 115°C the file was cured at 4.5 minutes and over-cured at 5 minutes. The test completed at 120°C shows that the file will take on average 3.5 minutes to cure and will be over-cured at 4.5 minutes.
For this test, all transfers were moved three (3) times during the curing process at different intervals. The orientations of the move were consistent across all tests where the file was originally placed centrally within the oven, then moved so that the top 50% of the image was protruding from the oven. This allows the ends of the image to cure without overcooking the centre of the print. This was then reversed for the other end. Finally, the print was repositioned to the original central location to cure any imperfections in the initial section. See table _ to see the time at which the file was moved.
100°C | 110°C | 115°C | 120°C | |
Full Coverage | 0 min | 0 min | 0 min | 0 min |
First 50% | 2 min | 2 min | 2 min | 1 min |
Second 50% | 4 min | 3 min | 3 min | 2 min |
Full Coverage | 6 min | 4 min | 4 min | 3 min |
Table 1 Movement Increments for Test Faces Curing Time vs Temperature
From this data it would be recommended that files with the level of ink coverage, are cured at 110°C – 115°C for the most consistent results.
Test Print #2 The bidirectional test print is W: 50mm x H: 50mm resulting in a maximum ink coverage of 25cm2. Due to the transparency, it is estimated to have 10cm2. | |
Test Print #3 The Alignment DTF RGB 200mm Test File is W: 290mm x H: 200mm meaning the total ink coverage will be 580cm2, it is estimated to be closer to 520cm2 due to transparencies. | Test Print #4 The test faces test print is W: 290mm H: 380mm resulting in a total ink coverage of 1140cm2. |